Aluminum strip is increasingly showing its irreplaceable position in modern industrial materials. With its light weight, high strength, excellent corrosion resistance and excellent processing performance, it is widely used in many key fields, including electronics, power, construction, automotive manufacturing and packaging industries. The popularity of this material not only reflects the physical and chemical advantages of aluminum itself, but also reflects the increasing demand for high-performance and sustainable materials in the manufacturing industry. For buyers seeking a reliable source of supply, choosing the best aluminum strip supplier, especially in the wholesale aluminum strip market, is the key to ensuring product quality and cost control. And with the rise of black anodized aluminum strips, its performance in decoration and functionality is constantly expanding new application boundaries.
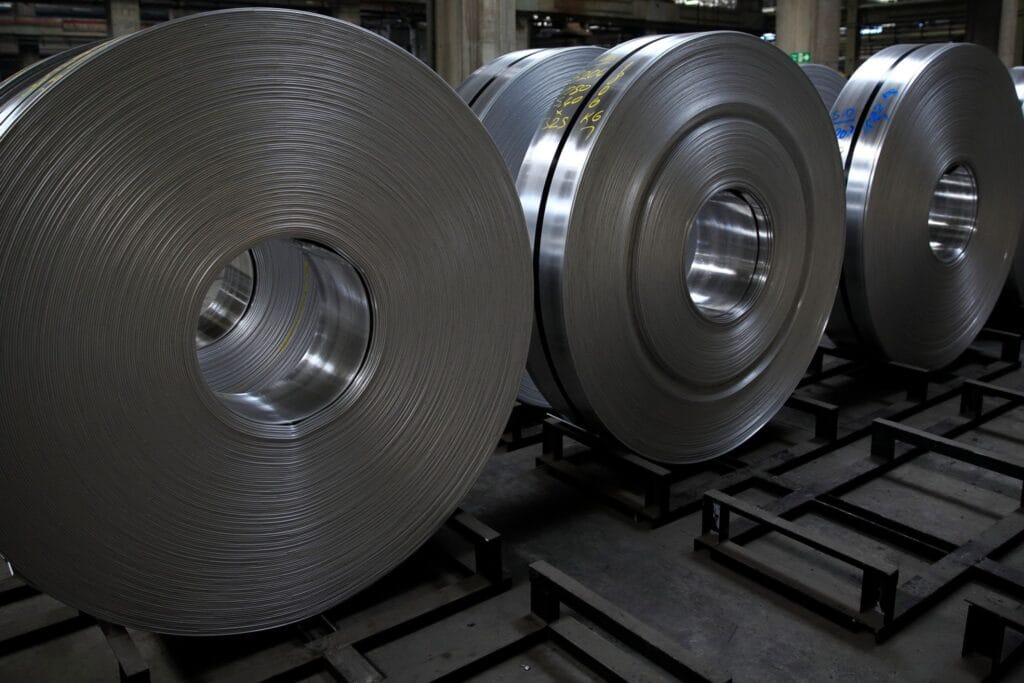
What is aluminum strip?
Aluminum strip is a precision-processed aluminum product, usually provided in the form of long rolls, with a flat strip cross-section. Compared with aluminum plates, the biggest feature of aluminum strip is that its width is relatively narrow, generally controlled between a few millimeters and hundreds of millimeters, while the thickness is usually maintained between 0.2mm and 3mm. It can be made of pure aluminum, such as 1050, 1060 and other series, or made of aluminum alloys, such as the common 3003, 5052, 8011, etc., depending on the final application scenario and performance requirements.
In actual use, the size, performance and state of aluminum strip (such as soft state O, semi-hard state H14, full hard H18, etc.) can be customized according to customer needs, so that it can be flexibly adapted to various deep processing scenarios. This material is very suitable for products that require post-processing such as bending, stamping, cutting and even anodizing due to its moderate strength and plasticity.
How are aluminum strip made?
The production process of aluminum strip is delicate and complex, usually starting with smelting and casting. First, the strictly proportioned aluminum ingots are melted at high temperature and formed into primary slabs by casting and rolling. These slabs then enter the hot rolling process, where they are rolled into thinner intermediate materials at high temperatures. Cold rolling is then used to further reduce the thickness and improve the strength and surface accuracy of the material.
When the material reaches the predetermined thickness, it is wound into a parent coil and enters the slitting process. At this stage, the parent coil is cut into aluminum strips of specified widths by high-precision slitting equipment. Finally, the finished product usually undergoes annealing to adjust its hardness and make it easier to form and weld.
Depending on the end use, the surface can also be specially treated, including brushing, anodizing, painting, or composite film layers. Among them, black anodized aluminum strips are aluminum strips that have been electrolytically oxidized to form a black oxide layer. They have both visual beauty and surface wear resistance, and are popular in the decoration field and electronic equipment housings.
What are the basic characteristics of aluminum strip?
The reason why aluminum strips are widely used in many industries is mainly due to its excellent material properties. First of all, its density is only about one-third of that of steel, which makes aluminum strips very attractive in structural designs that need to reduce weight, especially in the fields of transportation and aviation.
Secondly, aluminum naturally has good antioxidant properties. A dense and stable oxide film will quickly form on its surface, which effectively prevents further corrosion. This self-healing property allows it to maintain good performance in high humidity, acid rain or marine environments.
Electrical and thermal conductivity are also a highlight of aluminum strip, making it play an important role in the fields of electronics and electricity. In addition, aluminum strip has excellent forming ability and is suitable for a variety of processing methods such as stamping, deep drawing, and bending. It is particularly useful in manufacturing products such as transformer windings, cable sheaths, and automotive parts.
It is worth mentioning that its surface can be treated by oxidation, electroplating, and painting to enhance its aesthetics and functionality. For example, anodizing not only improves the surface hardness, but also gives aluminum strip a rich color selection. Black aluminum strip is developed on this basis and is widely used in electronic housings and high-end home decoration design.
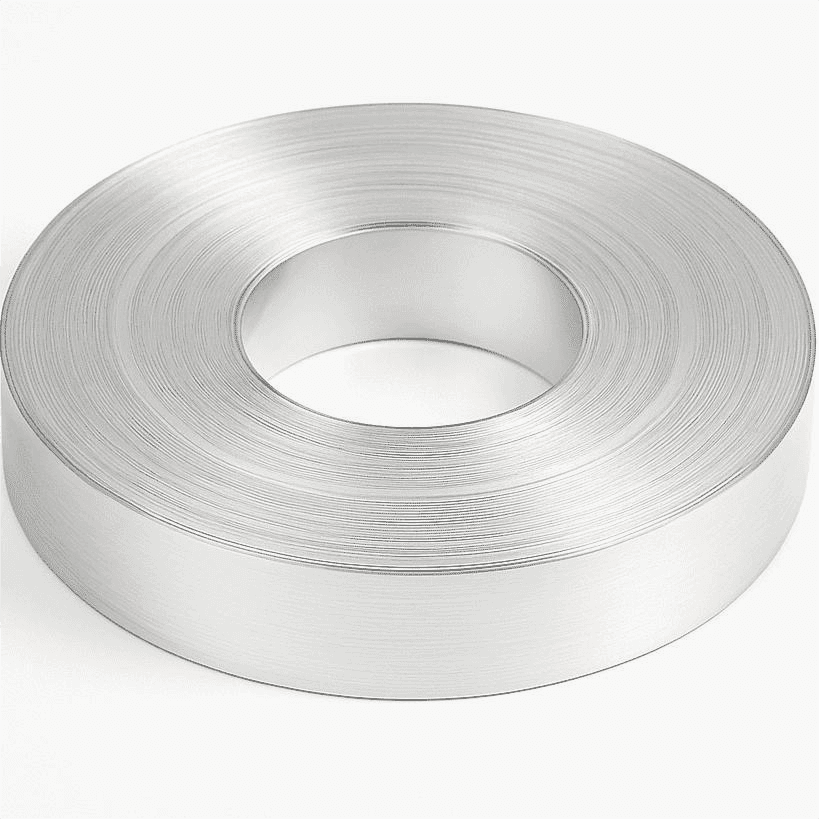
What are the common uses of aluminum strip?
The application scenarios of aluminum strip are extremely wide, covering almost all industrial fields related to material processing and finished product manufacturing. In the power industry, aluminum strips are often used in the manufacture of transformer windings, busbars, cable sheaths and other equipment. With its high conductivity and flexibility, it effectively reduces energy consumption and equipment volume.
In the field of automobile manufacturing, aluminum strips are used in fuel tanks, headlight brackets, filter components and other locations. Especially in the context of the rapid development of new energy vehicles, lightweighting has become one of the core design requirements, and aluminum strips are an important material to achieve this goal.
In addition, in the building decoration industry, aluminum strips are often used in aluminum-plastic panels, ceilings, curtain wall decoration and other fields. They are not only beautiful, but also have good weather resistance and anti-oxidation properties. Its excellent reflectivity also makes it an ideal material for LED lamp bases and solar reflectors.
The packaging industry uses its ductility and sealing properties to manufacture aluminum bottle caps, anti-theft seals, food composite packaging and other products. In precision manufacturing, such as electronic components and aerospace equipment, aluminum strips are also widely used due to their dimensional stability and controllable hardness.
What are the main specifications of aluminum strip?
In actual procurement and production, aluminum strips are usually defined and classified based on multiple technical parameters. The most basic is the material, which is generally distinguished by alloy series. For example, 1050 and 1060 of the 1000 series are suitable for occasions with high conductivity requirements, 3003 and 3105 of the 3000 series have better rust resistance, and 5052 of the 5000 series has both strength and weldability, suitable for higher strength occasions.
In terms of thickness, aluminum strips can be as thin as 0.03mm for high-precision electronic components, or as thick as 3mm or more for mechanical structural parts. The width can be customized from 10mm small strip products to 1600mm large coils. For most purposes, a width between 20 and 800mm is more common.
Aluminum strips are also divided into different hardness levels such as O state (completely annealed), H14 (semi-hard), and H18 (full hard) according to the processing state to adapt to different deep processing methods. Surface treatment is also an important indicator, including primary color gloss, brushed, coating, anodizing, etc. Among them, black anodized aluminum strip is gradually replacing traditional painted aluminum plate due to its low-key texture and scratch resistance, becoming the first choice in the field of mid-to-high-end customization.
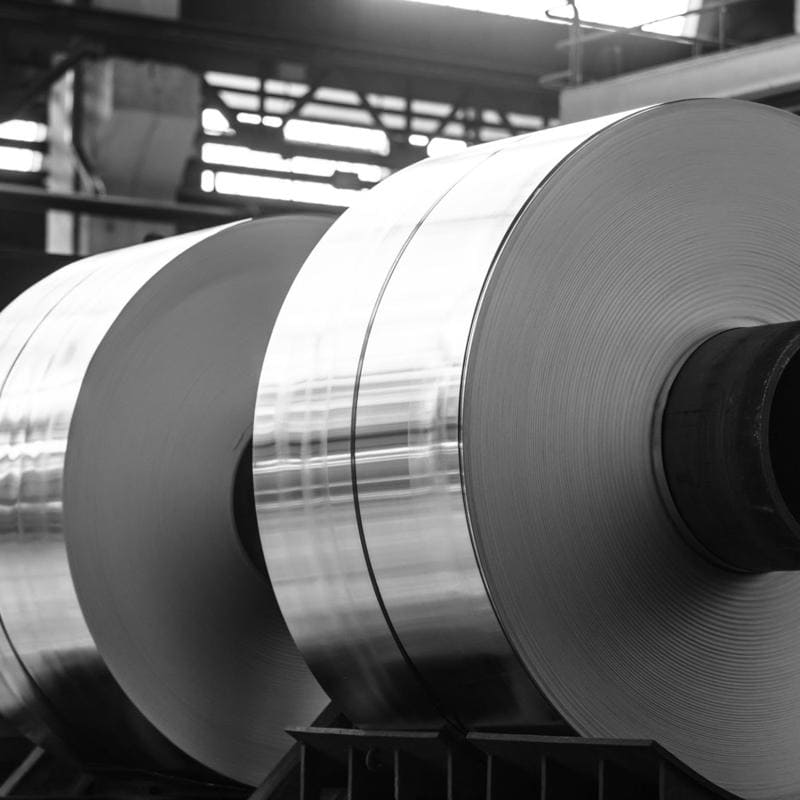
What are the advantages of using aluminum strip?
Compared with traditional metal materials, aluminum strips show significant advantages in many performance dimensions. The most direct is its light weight and high strength, which makes it competitive in applications that require structural load-bearing and are sensitive to weight. This is particularly critical for automobile manufacturing, rail transportation, and aviation equipment.
At the same time, aluminum strips have excellent formability and can maintain stable performance even under complex molds or high-speed stamping conditions, which greatly improves processing efficiency and finished product consistency. Its naturally formed oxide film can also greatly extend the service life and reduce maintenance requirements.
The recycling rate of aluminum is as high as more than 90%, which means that aluminum strips not only meet the concept of sustainable development, but also help companies achieve environmental protection goals and reduce raw material costs. In addition, the emergence of black anodized aluminum strips has brought new design possibilities to the construction, electronics and decoration industries. Its high-end matte texture not only improves the appearance of the product, but also enhances scratch and corrosion resistance.
Conclusion
With its exceptional versatility, lightweight structure, and ease of processing, aluminum strip has emerged as a key material driving innovation and manufacturing upgrades across multiple industries. Whether for electrical components, automotive parts, or architectural applications, its adaptability makes it indispensable. As a trusted aluminum strip supplier, ZGGD Metal offers high-quality solutions tailored to both standard and customized needs, supporting clients worldwide with reliable wholesale aluminum strip services.