When it comes to advanced aluminum alloys, few materials can rival the strength-to-weight ratio and performance of 7075 aluminum tube. Recognized for its exceptional mechanical properties, corrosion resistance, and machinability, this alloy has become a cornerstone in industries where structural reliability and lightweight design are paramount. Whether you’re sourcing materials for aerospace, defense, automotive, or high-performance sporting goods, understanding the nuances of 7075 tube can help you make informed procurement decisions.
This guide will walk you through everything you need to know—from composition and mechanical properties to shape selection, temper types, and how to evaluate 7075 aluminum tubing suppliers for your project needs.
Understanding 7075 Aluminum: What Makes It Unique?
The 7075 series aluminum alloy is primarily composed of zinc as its main alloying element, along with magnesium and copper, resulting in an exceptionally high-strength profile. Originally developed for aerospace applications, 7075 T6 aluminum tubing offers strength comparable to certain steels while maintaining aluminum’s hallmark lightness. Its tensile strength can exceed 74 ksi (510 MPa), while yield strength typically sits above 63 ksi (435 MPa), making it one of the most robust aluminum alloys available.
Despite its strength, it remains highly workable, especially in the T6 condition. This temper involves solution heat treatment and artificial aging, creating a balanced combination of hardness and ductility, ideal for structural applications where fatigue resistance and rigidity are essential.
Types of 7075 Tubing: Choosing the Right Form for Your Application
Aluminum tubing comes in various shapes and temper grades, each suited to different environments and performance requirements. Here’s a breakdown of the most common forms:
- 7075 T6 tube: This is the most popular variant, offering optimal tensile strength and rigidity. It is the go-to choice for aerospace structural frames, racing components, and other weight-critical assemblies where mechanical stress is high.
- 7075 T9 aluminum tubing: Less common but still relevant, this variant features slightly lower strength than T6, but with improved stress corrosion resistance. It’s often used in marine and industrial applications exposed to moisture and chemicals.
- 7075 aluminum pipe: Often manufactured with thicker walls and larger diameters, this form is favored in high-pressure systems and fluid transport within aircraft and high-performance vehicles.
- 7075 aluminum square tube: Ideal for building frameworks, support arms, and structures requiring rigid angular geometry. Its flat sides also make it easier to drill, machine, or weld compared to round tubing.
- 7075 aluminum round tube: This is the most versatile shape and is widely used across aerospace, automotive, and industrial manufacturing for both internal and external load-bearing parts.
For specialized projects, custom-shaped tubes like hexagonal, oval, or elliptical sections are also available from high-end 7075 aluminum tubing suppliers.
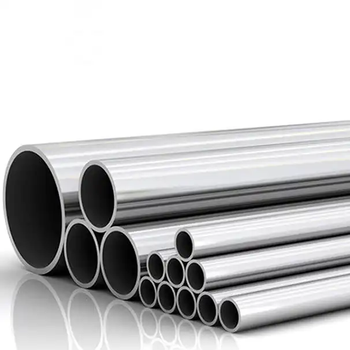
Key Applications: Where 7075 Aluminum Tubes Shine
Due to its superior mechanical performance, 7075 T6 aluminum pipe and other variants are frequently found in sectors that demand a careful balance between strength and weight:
- Aerospace and Aviation: Used in airframes, wing spars, hydraulic systems, and landing gear, where every ounce matters but failure is not an option.
- Defense and Military: From missile components to structural armor frames, the durability and weight savings of 7075 T6 aluminum tubing are invaluable.
- Automotive and Motorsports: Employed in chassis reinforcement, roll cages, and suspension components due to its stiffness and fatigue resistance.
- Sports and Recreation Equipment: High-performance bicycles, climbing gear, and aircraft-grade archery bows commonly incorporate 7075 tube for its lightness and ruggedness.
- Marine Engineering: T9 or T73 variants with added corrosion resistance are preferred for underwater or coastal structural designs.
Selecting the Right 7075 Tube: A Buyer’s Checklist
Before purchasing 7075 aluminum round tube or any other variant, it’s crucial to define your project requirements precisely. Here are key considerations to guide your selection:
- Mechanical Requirements
Choose 7075 T6 tube if maximum strength and minimal deformation under load are top priorities. Opt for T73 or T9 if stress corrosion cracking or environmental resistance is more critical. - Shape and Size
Evaluate whether round, square, or custom geometries better suit your assembly. For applications requiring precise fit or integration with other components, cold-drawn tubing ensures tighter tolerances. - Fabrication and Surface Treatment
Some suppliers offer anodizing, polishing, and CNC machining. Consider these if your application has cosmetic or additional corrosion protection needs. - Certifications and Compliance
Always verify that your material meets industry standards such as ASTM B241/B221 or AMS-QQ-A-225/9. Reputable 7075 aluminum tubing suppliers will readily provide material test reports (MTRs) and heat numbers for full traceability. - Sourcing Volume and Customization
For high-volume needs or unique specifications, direct negotiation with mill-level suppliers can offer better pricing, shorter lead times, and more customization flexibility.
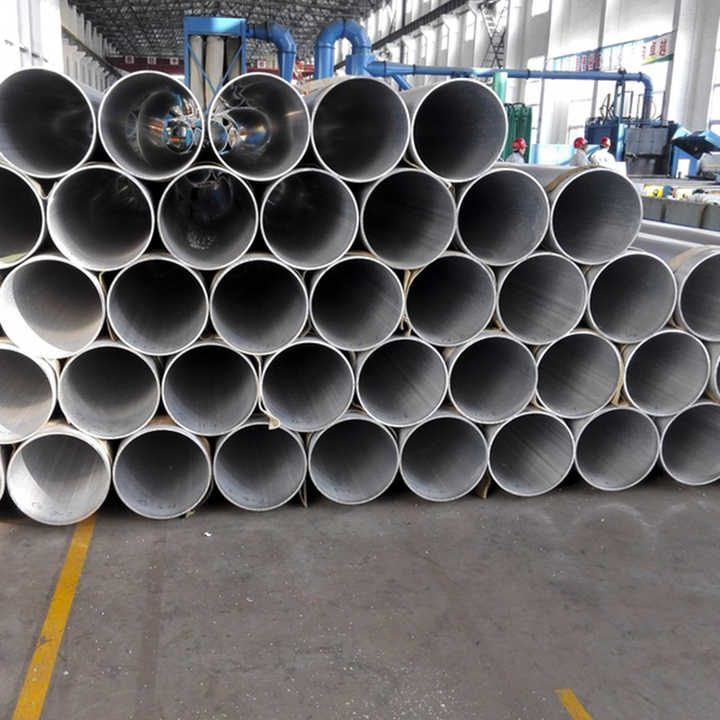
Where to Buy: Reputable 7075 Aluminum Tubing Suppliers
Sourcing quality tubing is just as critical as choosing the right material. Below are some vetted suppliers known for delivering high-grade 7075 aluminum pipe and 7075 square tube options:
- TW Metals – Specializes in aerospace-grade aluminum tubes with certified traceability and cut-to-length options.
- Online Metals – Offers an easy-to-navigate online catalog for 7075 aluminum square tube, round, and rectangular sections.
- ZGGDMETAL – An industry leader in heat-treated 7075 aluminum tubing with multiple temper options and export-ready documentation.
- Aircraft Extrusion Company – Provides custom profiles and shapes suitable for highly specialized engineering requirements.
- ThomasNet Listings – A comprehensive directory to locate distributors offering local inventory and just-in-time delivery services.
Conclusion: Why 7075 Aluminum Tubing is a Strategic Investment
Whether you’re building a racing machine, an aircraft, or a lightweight structural platform, investing in 7075 T6 aluminum pipe or other high-strength variants of this alloy ensures reliability under demanding conditions. Its unmatched strength-to-weight ratio, paired with versatility across shapes and processing techniques, makes it one of the most valuable materials for forward-thinking engineers and manufacturers.
By understanding the various product forms, temper grades, and sourcing strategies outlined in this guide, buyers can confidently select the best 7075 aluminum tube for their specific needs—reducing cost overruns, ensuring structural integrity, and maximizing performance in real-world applications.