Introduction: Why Aluminum Tubes Matter
Aluminum tubes have become a cornerstone material across various industries—ranging from aerospace and transportation to architecture and marine engineering. Their unique blend of lightweight performance, corrosion resistance, and mechanical strength makes them a top choice in both structural and non-structural applications.
At zggdmetal, we understand the critical role aluminum tubing plays in modern manufacturing and infrastructure. This comprehensive guide will help you better understand the properties, classifications, and practical uses of aluminum tubes—so you can choose the right product with confidence.
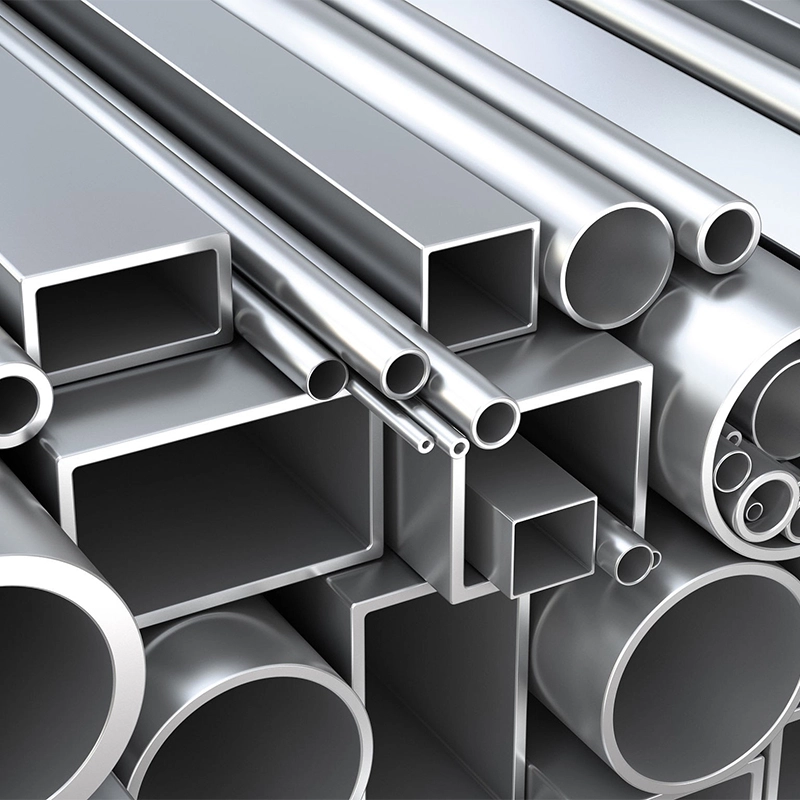
What Is an Aluminum Tube?
An aluminum tube is a hollow, cylindrical product manufactured from pure aluminum or aluminum alloy. It’s engineered to offer high strength-to-weight ratios, resist corrosion, and conduct heat or electricity efficiently.
Unlike steel, aluminum is significantly lighter while offering comparable structural capabilities. These characteristics have positioned aluminum tubing as a sustainable, efficient material choice for modern engineering solutions.
Popular Aluminum Alloys for Tubing
Not all aluminum tubes are created equal. The alloy you choose affects the tube’s formability, strength, corrosion behavior, and suitability for specific environments.
Here’s a breakdown of some widely used aluminum alloys:
6061 | Versatile, weldable, good corrosion resistance | Aircraft, frames, bridges |
6063 | Smooth finish, excellent extrudability | Window frames, architecture |
7075 | Exceptional strength, limited weldability | Aerospace, defense parts |
2024 | High fatigue resistance | Aircraft structures |
5083 | Marine-grade, excellent saltwater resistance | Boats, offshore platforms |
Types of Aluminum Tubes
Aluminum tubing is available in different shapes and manufacturing styles, each tailored to specific performance needs:
1.Round Tubes
The most common form, used for fluid transport systems, handrails, and load-bearing applications.
2.Square & Rectangular Tubes
Ideal for architectural frames, enclosures, and structural components where flat surfaces are preferred.
3.Seamless Tubes
Produced without welds, offering superior pressure resistance and structural integrity—essential for hydraulic or aerospace use.
4.Drawn Tubes
Cold-drawn tubing features tighter tolerances, improved strength, and a smoother finish—frequently used in precision equipment.

Surface Treatment Options
Aluminum’s natural corrosion resistance can be further enhanced through various surface treatments. These finishes not only improve durability but also contribute to aesthetics:
Anodizing – Electrochemical process that increases surface hardness and allows for color finishes.
Powder Coating – Adds a protective, decorative layer resistant to scratches and UV damage.
Brushed Finish – Provides a matte, linear grain ideal for architectural design.
Mill Finish – Raw and untreated, suitable for further processing or industrial use.
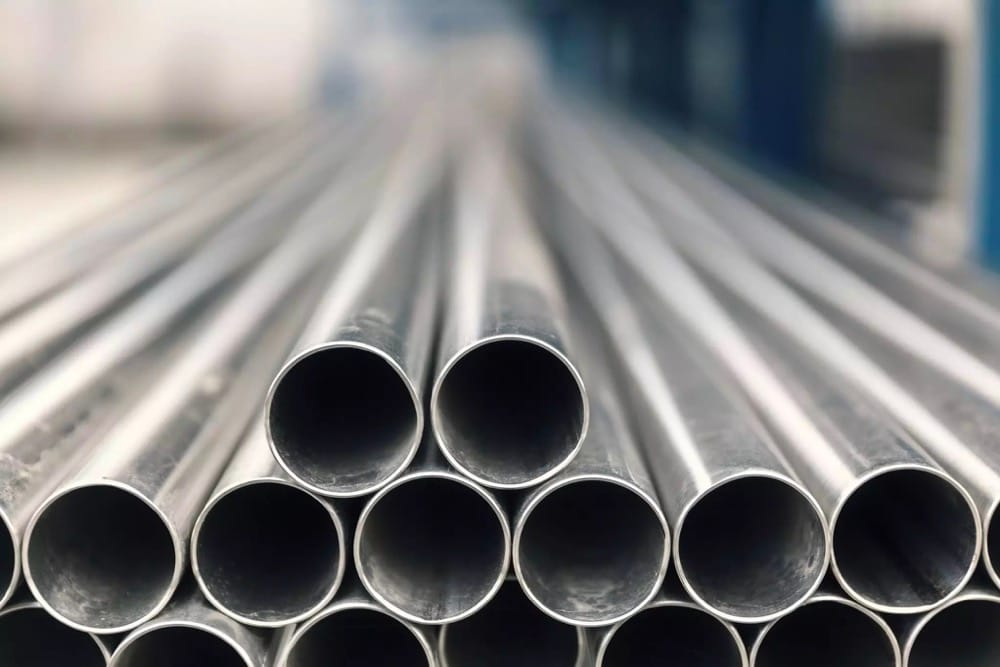
Key Industries Using Aluminum Tubes
The versatility of aluminum tubing makes it suitable for applications in nearly every major sector:
- Automotive: Used in fuel lines, heat exchangers, roll cages, and structural components.
- Aerospace: Critical for aircraft frames, landing gear, and hydraulic systems.
- Construction: Found in window and door systems, curtain walls, supports, and railings.
- Marine: Ideal for shipbuilding, marine ladders, masts, and corrosion-prone areas.
- Electronics: Utilized in heat sinks, protective enclosures, and lightweight framework.
How to Choose the Right Aluminum Tube
Selecting the right aluminum tube starts with understanding your project’s specific requirements. Here’s a step-by-step approach:
1.Define the Application: Will it be structural, decorative, or used in high-pressure environments?
2.Select the Alloy: Match alloy properties with your performance and corrosion resistance needs.
3.Choose the Shape: Round for flow and strength, square/rectangular for frameworks.
4.Determine the Finish: Consider environmental exposure and aesthetic requirements.
5.Check for Certifications: Look for compliance with standards like ASTM, ISO, or military specs if required.
Why Partner with zggdmetal?
At zggdmetal, we supply premium-quality aluminum tubes tailored for global industries. Here’s why manufacturers choose us:
- Full range of alloys and sizes in stock
- Custom cut-to-length and OEM capabilities
- Precision manufacturing with ISO-certified quality
- Short lead times and international shipping
- Competitive B2B pricing with technical support
Whether you’re sourcing for aerospace assemblies or architectural frameworks, our team can help you find the right solution fast and reliably.
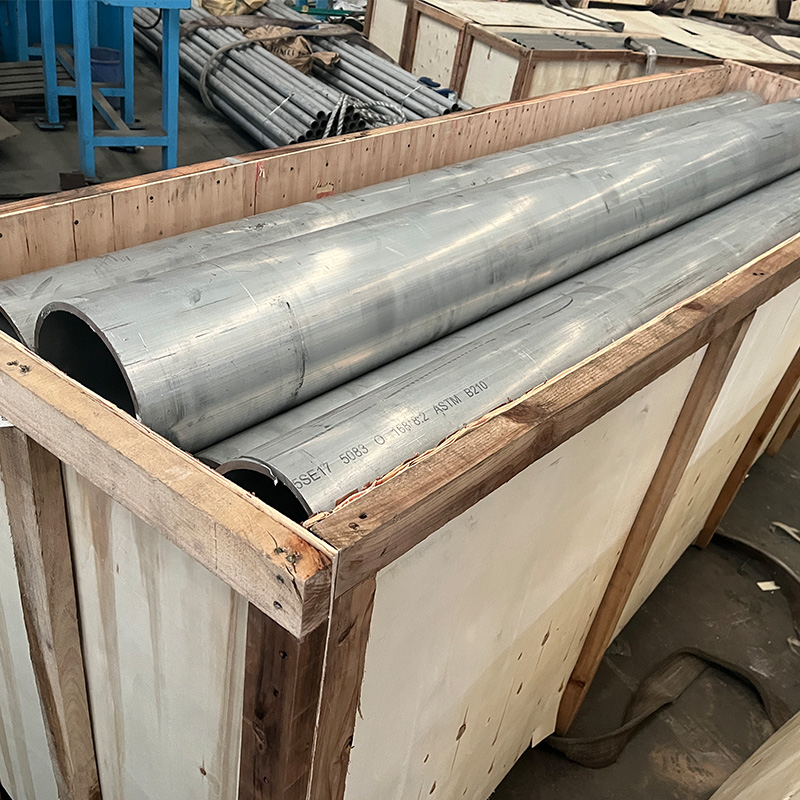
Conclusion: The Aluminum Tube Advantage
From strength-to-weight efficiency to corrosion resistance and thermal performance, aluminum tubes offer a host of engineering benefits. By selecting the appropriate alloy, shape, and finish, you can ensure optimal functionality and longevity for your application.
Need help selecting the right aluminum tube? Contact zggdmetal today—your reliable partner in industrial aluminum solutions.