What is aluminum tube?
Aluminum tubes are hollow cylindrical profiles made from aluminum or aluminum alloys. These tubes come in various cross-sectional shapes such as round, square, or rectangular, and are valued for their combination of light weight, strength, and excellent corrosion resistance. Whether used in construction, transportation, or thermal systems, aluminum tubes have become a vital material across many industries.
Their versatility stems not only from the base properties of aluminum, such as high thermal conductivity and low density, but also from the wide variety of alloy grades available on the market. For instance, 1100 aluminum tube is known for its exceptional corrosion resistance and workability, making it suitable for chemical equipment and food handling systems, while 7075 aluminum tube is prized for its strength and is often found in aerospace applications.
Aluminum tubes are also a preferred solution where formability and weight reduction are essential. The combination of structural integrity with reduced mass makes them particularly useful in industries that rely on energy efficiency and high performance, such as automotive and marine manufacturing.
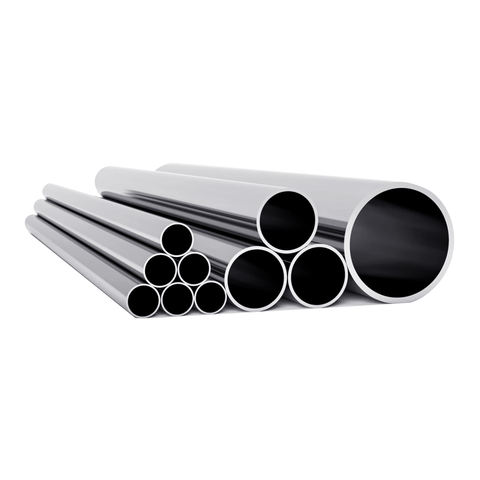
How are aluminum tubes made?
The manufacturing process of aluminum tubes begins with selecting the appropriate alloy, depending on the intended application. Common alloys include 1100, 6061, 5086, and 7075, each offering specific performance traits.
One of the most common production techniques is extrusion, where heated aluminum billets are forced through a die to create seamless tubes with uniform cross-sections. This process ensures strength consistency and is ideal for high-pressure applications. For tubes requiring tighter tolerances, cold drawing or cold rolling is often used post-extrusion to refine the dimensions and enhance surface finish.
Another method involves welded aluminum tubes, where aluminum sheets or strips are rolled and then joined using high-frequency or TIG welding. Though not as strong as seamless tubes, welded tubes offer flexibility in size customization and are generally more cost-effective, especially for wholesale aluminum tubes.
After shaping, tubes typically undergo various treatments such as heat tempering (e.g., T6 or H32 conditions) and surface finishing processes including anodizing, powder coating, or polishing. These post-processing steps help improve appearance, durability, and corrosion resistance—key factors especially for outdoor or marine environments where materials are exposed to moisture and salt.
What are the basic characteristics of aluminum tubes?
Aluminum tubes boast a unique set of mechanical and physical properties that make them highly desirable across multiple industries. Their low density translates to significant weight savings, particularly beneficial in transportation-related applications where efficiency and fuel economy are critical.
In addition to their lightweight nature, aluminum tubes exhibit excellent corrosion resistance, especially alloys like 5086 aluminum tube, which is often used in marine environments due to its superior resistance to saltwater. This corrosion resistance arises naturally from the formation of a thin oxide layer on the aluminum surface, which acts as a protective barrier.
Another key property is thermal and electrical conductivity. Aluminum conducts heat and electricity well, making it a preferred material for heat exchangers, radiators, and wiring enclosures. In industries requiring high conductivity, like electronics or HVAC systems, aluminum tubing provides both function and form.
Furthermore, aluminum tubes are easy to fabricate, whether by cutting, drilling, welding, or bending. This machinability contributes to their popularity among manufacturers and engineers. The ability to apply various finishes also enhances their suitability for aesthetic architectural applications.
From a sustainability perspective, aluminum is 100% recyclable without loss of quality, contributing to reduced environmental impact and aligning with global trends toward greener manufacturing practices.
How do aluminum pipes differ from steel pipes made of other metals?
When comparing aluminum tubes to those made from steel or other metals, several fundamental differences emerge. The most noticeable is weight—aluminum weighs roughly one-third that of steel, making it far easier to handle, ship, and install, especially in large-scale projects.
Aluminum is also more corrosion-resistant than carbon steel or even stainless steel in many cases. While steel typically requires protective coatings to withstand corrosion, aluminum forms its own oxide shield naturally, offering built-in protection against environmental elements.
From a mechanical standpoint, steel generally offers higher tensile strength, but modern aluminum alloys such as 7075 aluminum tube can rival low- to mid-grade steels in terms of structural performance. However, aluminum’s superior flexibility and fatigue resistance often make it a better choice in applications involving vibration or dynamic loads.
Additionally, aluminum is non-magnetic, which can be a significant advantage in electrical applications or environments where magnetic interference must be minimized. Its better thermal conductivity also makes it a smarter option in heat-sensitive installations.
Finally, aluminum tends to be easier to process and form, saving both time and cost in fabrication. For industries requiring customized dimensions or large batch production, sourcing from the best aluminum tube supplier ensures consistent quality and scalability.
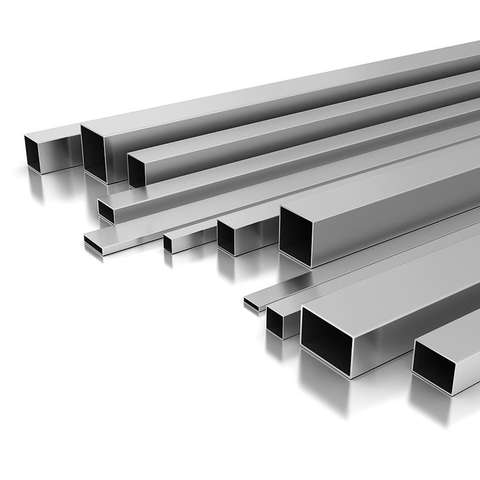
What are the common uses of aluminum tube?
Aluminum tubes are widely used in applications where strength, lightness, and corrosion resistance are essential. In the automotive industry, they serve in exhaust systems, crash management components, and chassis structures. Their contribution to vehicle weight reduction helps improve fuel efficiency and performance.
In the marine sector, 5086 aluminum tube is commonly used for boat hulls, railings, and masts due to its resistance to seawater. It is also suitable for offshore structures and marine hardware that require long service life in harsh conditions.
Aerospace manufacturers utilize 7075 aluminum tube in critical structural components like landing gears and wing supports, where both lightweight and high strength are vital. This alloy, known for its excellent fatigue resistance, is particularly suited for high-load-bearing parts.
In construction, aluminum tubes are used in window frames, handrails, scaffolding, and load-bearing beams. Their clean appearance and resistance to rust make them ideal for architectural facades and modern infrastructure projects.
The HVAC and energy sectors depend on aluminum tubes in the design of heat exchangers, solar panel frames, and duct systems. Their thermal efficiency and ease of installation make them the material of choice for such systems.
Other notable uses include medical equipment, fitness machines, furniture framing, and even food processing lines, where 1100 aluminum tube is favored for its high purity and hygiene compliance.
What are the main specifications of aluminum tube?
Aluminum tubes come in a variety of grades and dimensions to suit different engineering requirements. The choice of alloy significantly affects mechanical properties. For example, 1100 aluminum tube is soft and corrosion-resistant but not suitable for structural applications, whereas 6061 or 7075 are much stronger and more versatile.
Available shapes include round, square, and rectangular profiles, each serving different structural or functional roles. Common outer diameters range from a few millimeters up to several hundred millimeters, with wall thicknesses tailored to strength needs—standard ranges run from 0.2 mm to over 20 mm for industrial-grade tubes.The characteristics of aluminum round tubes: balanced structure, strong pressure bearing capacity, easy to bend and shape, good torsion resistance. Mainly used in railings, handrails, awning brackets: beautiful appearance, easy to process into curved surfaces or angles.
The characteristics of aluminum square tubes are regular structure, uniform force, convenient connection, and neat appearance. Mainly used in industrial frames and automation equipment brackets: such as assembly line skeletons and machine tool frames. The characteristics of aluminum rectangular tubes
are that one side has higher strength, which is suitable for large spans or structures with specific force directions; it is easy to fit the wall or narrow space. Mainly used in building curtain wall back frames and keel systems: suitable for components that need to bear glass or aluminum plates.
Tubes are also classified by temper designations (such as O, T6, H32) that indicate the processing method and resulting strength or hardness level. The choice of temper affects weldability, machinability, and formability.
Length options vary by supplier but typically fall into standard lengths such as 6 meters. However, bulk orders through wholesale aluminum tubes channels often allow for customized cuts and packaging. Reputable aluminum tube suppliers also offer certificates of compliance, traceability, and technical support to ensure consistent product quality across projects.

What are the advantages of using aluminum tube?
In addition to material performance, there are many advantages to choosing aluminum tubes. One of the most obvious advantages is that it is lighter than steel and can maintain the original metal strength, which can provide excellent structural support and load-bearing capacity.
Aluminum is corrosion-resistant, ensuring its durability in outdoor or corrosive environments, reducing the need for coating or maintenance. This is particularly important in applications such as marine or coastal infrastructure.
Another significant advantage is processability. Whether by cutting, bending or welding, aluminum tubes can be cut and bent on site or in the workshop by cutting machines or press bending machines, thereby reducing production downtime. Aluminum tubes can be subjected to various surface treatments, such as anodizing, powder coating or brushing, which has a certain ornamental effect.
Conclusion
Aluminum tubes are a cornerstone of modern industry, offering the perfect balance of lightness, durability, and adaptability. Whether you’re designing high-performance machinery, reinforcing architectural structures, or fabricating custom parts, aluminum tubing delivers reliability and flexibility across all sectors.
At zggdmetal, we supply a wide range of aluminum tubes tailored to meet international standards and project specifications. Contact us today to get expert advice and discover the best aluminum tube solution for your business.